Liquid crystal elastomers make morphing fabric
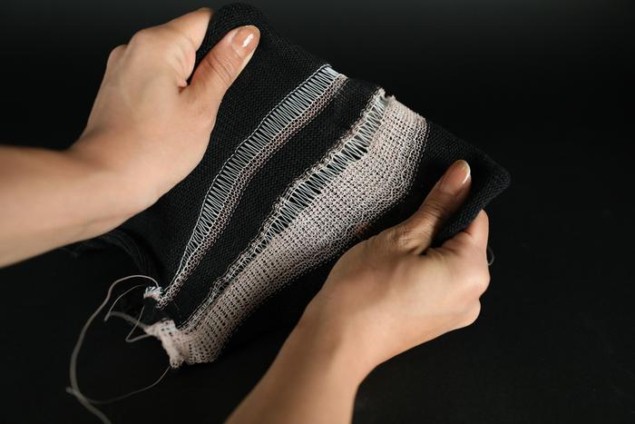
A new type of fibre reversibly changes its shape in response to temperature and can be spun into threads to make entire morphing garments. Potential applications for the technology include compression garments for post-surgical recovery, adaptive architectural interiors and even clothing that “hugs†its wearer on activation.
The new fibre was developed by researchers at the Massachusetts Institute of Technology (MIT) and Northeastern University, US, and is compatible with standard textile manufacturing techniques, including industrial and non-industrial sewing/knitting machines and looms. Unlike current shape-changing fibres, it can be combined with conductive thread that heats up when an electric current is applied to it.
Led by Jack Forman, a PhD student in MIT’s Center for Bits and Atoms & Tangible Media Group, the team made the fibre by synthesizing a liquid crystal elastomer (LCE) in a two-stage, one-pot, thiol-acrylate/ene “click†reaction. Although molecules in liquid crystals flow like a liquid, they can also stack into a periodic crystal arrangement. In the material studied in this work, molecules in the crystal become misaligned when the fibre is heated. This misalignment pulls the elastomer network together and causes the material to contract. After the heat is removed, the fibre returns to its original length.
As part of a graduate-level course (MAS.865 Rapid-Prototyping of Rapid-Prototyping Machines: How to Make Something that Makes (almost) Anything), Forman also developed and constructed a machine that can spin the fibre into a continuous thread. The machine heats the LCE resin and slowly squeezes it through a nozzle. As the fibre extrudes, it is cured with UV light. In the final stage, the fibre is coated with a slippery film and cured again. The result is a strong and smooth fibre that is then collected into a top pool and dipped in powder so that it can pass easily into textile manufacturing machinery.
The complete synthesis and spinning process takes about 24 hours from start to finish, and it generates a ready-to-use fibre about a kilometre in length. But Forman admits that developing it was not all plain sailing. “Since the resin and the machine were both made in-house, we had so much more freedom but also a larger scope of issues to debug,†he tells Physics World. “At times it was impossible to tell if an experiment failed because the machine was misbehaving or the material. Both had to be debugged, as there was no room for faulty electrical connections or a lack of precision during synthesis.â€
Fibre can be knit, woven and embroidered
As well as fully detailing the manufacturing process in UIST ’23: Proceedings of the 36th Annual ACM Symposium on User Interface Software and Technology, the researchers have made the design of their custom spinning machine open-source. In the long run, they hope the fibre will become something people can easily buy, just like a ball of yarn. “One can imagine a world where adaptive fabrics made from such fibres are part of everyday life,†Forman says.
To date, the team has used an industrial knitting machine to make several garments from the fibre. These include a sports bra that tightens when the wearer exercises, a silent morphing curtain and a lamp that blooms when switched on.
Spinning a sustainable fashion revolution: meet the physicists turning wood into clothes
“We also made a sweater for my dog so that when she barks in my office, I press a button on my phone and it gently compresses around her to give her the feeling of being hugged,†Forman adds.
The next step, he says, will be to scale up the production process. “We are now exploring larger ‘human-sized’ devices and wearables. It takes 150 m of fibre to make a pair of jeans so it is a good start that we can reliably make 1 km of fibre in an afternoon.â€
Other members of the team were Ozgun Kilic Afsar, Neil Gershenfeld, Zachary Gordon, Cedric Honnet, Hiroshi Ishii, Akshay Kothakonda, Rosalie (Hsin-Ju) Lin, Sarah Nicita and Liu Yang at MIT, as well as Kristen Dorsey and Megan Hofmann at Northeastern University.